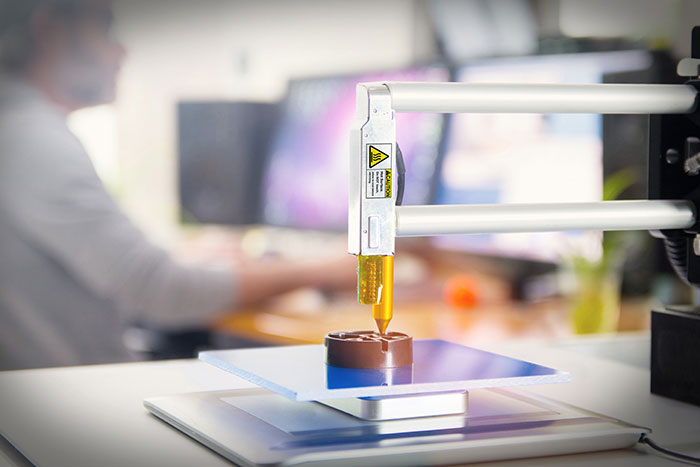
Rapid prototyping, also known as additive manufacturing, is a prototyping method that makes three-dimensional physical objects from a digital file. A 3D printer lays down many layers of material in succession, building the part as it goes.
What are the different types of rapid prototyping?
There are multiple techniques available for rapid prototyping, with new technologies becoming available regularly. Here are the top four methods we use when building prototypes:
Stereolithography (SLA)
Stereolithography is an additive manufacturing process where UV light is applied to a photopolymer resin causing it to solidify. SLA has the advantage over other rapid prototyping methods of producing watertight and clear parts
Selective laser sintering (SLS)
Selective laser sintering involves using a high-power laser to fuse a powdered material, such as nylon, into a 3D shape. SLS is commonly done using nylon producing strong part.
Fused deposition modeling (FDM)
Fused Deposition Modeling involves extruding thermoplastic resin through a nozzle onto a platform. The layers are applied using a cross-wise pattern that hardens as it cools. FDM is what people most often envision when they think of 3D printing as it is the least expensive method and easy to use.
Direct metal laser sintering (DMLS)
Direct Metal Laser Sintering is similar to SLS in that it uses a laser to fuse powder into a solid material. As the name suggests, the difference lies in that DMLS involves using metallic powders. Parts produced using DMLS are durable enough to work as a functional prototype as well as in end-use production.
How does rapid prototyping work?
Regardless of building material or printing methods, to make a 3D printed object, you need to start with a 3D digital model. This model is often in the form of a ComputerAided Design (CAD) file built using Solidworks or ProEngineer software. The CAD file is then run through another software that converts the 3D object into hundreds or thousands of 2D slices. The 3D printer then builds the object, layer by layer, using these 2D slices as blueprints.
What are some advantages of rapid prototyping?
- Low-cost
- Faster than traditional machining methods
- Can make almost any complicated geometry, including a negative space within your object
What are some disadvantages of rapid prototyping?
- Lower resolution than traditional metal machining
- Grain direction matters as the part is weaker across the grain axis
- Laser or nozzle size determines tolerance. For FDM parts, this is currently .007” thick
- Part size is limited by the machine’s platform
What is an example of rapid prototyping?
Synectic has extensive 3D printing experience developing prototypes and manufactured products using our in-house FDM machine. If you are not sure if rapid prototyping is the best method for your project or need help developing your prototypes, contact us and we would be happy to help.
About Synectic Product Development: Synectic Product Development is an ISO 13485 certified, full-scale product development company. Vertically integrated within the Mack Group, our capabilities allow us to take your design from concept to production. With over 40 years of experience in design, development, and manufacturing, we strive for ingenuity, cost-effectiveness, and aesthetics in our designs. Learn more about our prototype development services and see how we can help your next project.