GET READY FOR PRODUCTION WITH DESIGN FOR MANUFACTURING
Move your design from prototype development to manufacturing with DFM/DFA. DFM/DFA stands for design for manufacturing and design for assembly, respectfully. During this part of product development, specialized engineers redesign your final prototype for volume manufacturing, optimizing for fabrication method and cost. Synectic’s extensive design for manufacturing process includes the following:
- First, our experienced manufacturing engineers evaluate each component and decide on the best method for fabrication based on design and cost.
- Next, we redesign each part for the chosen fabrication method.
- Then, we create pre-production drawings with tolerances and material selection.
- We also complete a tolerance stack-up analysis, ensuring your parts assemble correctly during production.
- We then price each part in a preliminary costed BOM or bill of materials, so you know your final product costs.
- Before we wrap up DFM, we conduct a detailed design review for your final approval.
- Finally, we produce and test several machined pre-production units. These units ensure that none of the manufacturability changes affect overall performance. These units are also used to produce initial detailed work instructions for the assembly team.
After this extensive process, you will have a high-quality design optimized for manufacturing that is reliable, functional, and ready to scale up in our new product introduction area.
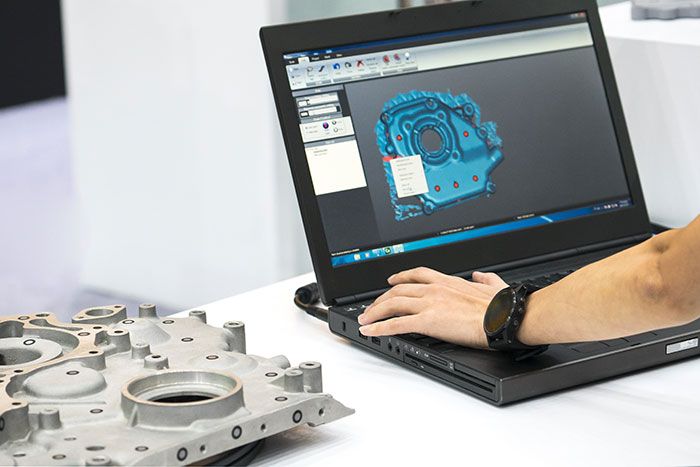
OPTIMIZE YOUR DESIGN FOR MANUFACTURING
Design for Manufacturability
Design for Assembly
Design for Cost Reduction
Design for Cost Reduction
Minimize Part Count
Design for Testability
Design for Flexibility
Design for Flexibility
OUR DESIGN FOR MANUFACTURING PROCESS
DFM/DFA Refinements
Our design for manufacturing process starts by improving your components for the chosen manufacturing process. We use end-user feedback, testing, and analysis to fine-tune your design for better manufacturability and cost savings. With plastic injection molding, our engineers will optimize the design to make it moldable, such as combining parts, adding structures like ribbing, radii, draft angles, and gates, adjusting wall thickness for the chosen material, and designing for the direction of mold pull. These efforts enhance manufacturability, assembly, and cost savings.
Tolerance Analysis
Once the design refinement process is complete, our manufacturing engineers conduct a tolerance analysis. This analysis assesses the critical function fits and assembly stack-ups that are most likely to reduce risks in the design. Through this analysis, we ensure that all vital parts will function seamlessly once they are manufactured. Our systematic process involves evaluating the impact of manufacturing and dimensional variations, as well as uncertainties on the final product’s quality, functionality, and performance. We use this information to determine how variations in individual components or processes could accumulate and affect the overall product’s fit, form, and function. Ultimately, the goal of tolerance analysis is to guarantee that the final assembled product meets the desired specifications and performance requirements, even when considering manufacturing variability.
Supplier Selection
During design for manufacturing, we will work with you to select suppliers who are reliable and consistent sources of materials, components, and services. We use a variety of criteria to choose our suppliers, such as verifying their ISO certifications, ensuring they can produce parts to specification, adhering to good manufacturing practices, and having internal systems in place to support production. We also consider their experience, quality standards, delivery reliability, capabilities, and pricing. By carefully selecting our suppliers, we can improve the manufacturing process and ensure timely access to necessary resources.
Material Selection
In addition to choosing the right supplier, we’ll assist you in selecting appropriate materials for each component based on its intended use, performance requirements, and manufacturing processes. Our material selection process takes into account factors such as strength, robustness, sterilization, biocompatibility, working conditions, fabrication method, and assembly methods. It’s important to note that different materials have unique properties, costs, and manufacturability characteristics. Our goal is to choose materials that are compatible with the manufacturing techniques and assembly methods, while achieving the desired quality and cost objectives.
Manufacturing Flow Chart
We will prepare a manufacturing flow chart, called a process flow diagram, that details the sequential steps, activities, and interactions involved in the manufacturing process of your product. This visual display offers an organized and concise summary of how raw materials are converted into your finished product, highlighting the order of operations, decision points, and pathways within the production workflow. A comprehensive manufacturing flow chart allows us to pinpoint bottlenecks, inefficiencies, and chances for process enhancement, leading to a smoother production process.
MFMEA
One of the last actions in the DFM process is performing an MFMEA, which stands for Machinery Failure Mode and Effect Analysis. It is a systematic approach to identifying potential failure modes in the manufacturing process and assessing their potential impact on your product’s quality, reliability, and safety. MFMEA helps us prioritize which failure modes to address first and guides corrective actions to prevent or mitigate them. In short, we review each manufacturing operation and assign a risk score. If the risk score exceeds a specified threshold, we recommend building a fixture or implementing a test to address this risk.
Design Transfer
Once your design for manufacturing is complete, we will prepare it for transfer to our new product introduction area. Here, we will upscale your design for full-scale contract manufacturing. Since we conduct new product introduction on-site, the transition from R&D to production is seamless, and we can quickly and efficiently resolve any issues identified post-transfer. If you opt to work with an external manufacturer, we will collaborate with their manufacturing teams to facilitate a smooth transfer from engineering to production.
DESIGN FOR MANUFACTURING FREQUENTLY ASKED QUESTIONS
Design for manufacturing, also known as DFM, is an engineering process that optimizes your product design for manufacturing. It helps reduce manufacturing costs, improve product quality, shorten time-to-market, and enhance overall manufacturing efficiency by addressing potential issues early in the design process.
During design for manufacturing, our team of engineering and manufacturing experts work closely together to optimize your product design for efficient production. We meticulously evaluate critical aspects such as materials, manufacturing processes, tolerances, assembly methods, and cost considerations. We will refine your design to ensure compatibility with manufacturing capabilities, minimize part count, and enhance overall quality. During this time, we also identify and address potential issues or challenges that may arise during manufacturing and assembly and put solutions in place. We aim to create a well-balanced design that aligns functionality with manufacturability, aiming to reduce costs, improve production efficiency, and deliver a high-quality product to the market.
Design for manufacturing is a complex and vital part of developing your product. It is not something you want to skip or take shortcuts on. Because of this, DFM usually takes several weeks. However, the DFM process can take months for more complex products or projects involving intricate designs, specialized manufacturing processes, or extensive iterations.
Unless you are an experienced manufacturing engineer, we do not recommend you undertake design for manufacturing by yourself. When done correctly, DFM requires teams of experts working together for weeks or months to ensure a quality product. We recommend pairing with a qualified design for manufacturing expert like Synectic, who can get your product to market quickly.
After design for manufacturing, your product will move to our new product introduction area. There, we build your first units and test them. The process gradually scales up production until you hit full-scale contract manufacturing.
To receive a quote, kindly fill out the contact form, and one of our manufacturing specialists will contact you about your project.